Amidst the ongoing challenges posed by supply chain disruptions and the relentless rise in manufacturing costs attributed to fluctuating raw material prices and the imperative for manufacturers to align with industrial and technological advancements, there’s a growing impetus among automotive manufacturers to prioritize cost reduction strategies. This shift aims to bolster their competitiveness, enhance sustainability, and maximize overall profits.
Key to this endeavor is the adoption of efficient materials and the optimization of the production process through meticulous data analysis. Moreover, forging robust partnerships with reliable suppliers is essential to meet goals and objectives while adhering to stringent metrics. Embracing automation technologies not only streamlines operations but also mitigates the impact of escalating regional wages. Furthermore, strategic decisions regarding outsourcing and offshoring can further drive down costs, ensuring sustained profitability amidst a dynamic manufacturing landscape.
Here are four ways that the automotive industry will be able to cut costs and save money in the near future:
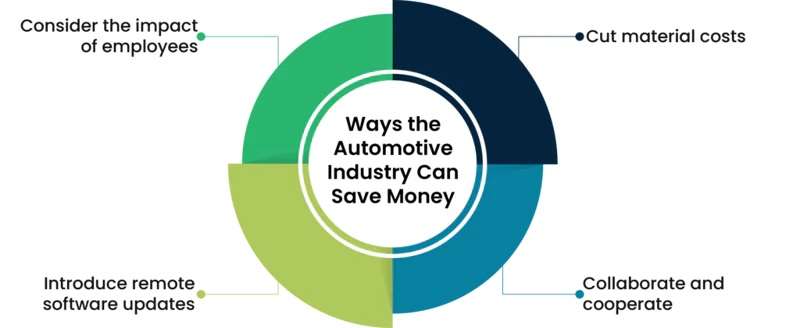
- Consider the impact of employees: Having a highly skilled and trained workforce is essential for cost reduction. Employees that introduce errors, do not adhere to company spend policies, or who are not trained on procedures and practices properly can cause a company to incur significant costs. It’s important that employees receive extensive training and are regularly assessed to determine their qualifications, suitability, and competency regarding their day-to-day work activities, especially for jobs with a higher risk of danger. Reducing employee errors, increasing employee satisfaction for automotive jobs, and ensuring your workforce is appropriately skilled will help to reduce costs as well as increase safety and employee retention. This focus on human capital plays a crucial role in achieving cost reduction in the automotive industry.
- Introduce remote software updates: Enabling wireless, over-the-air software updates to telematics and infotainment systems has the potential to save the automotive industry more than USD 30 billion (in America alone) by 2022, according to a study by IHS Automotive. This method of remote software fixes is significantly less expensive than updates done using a cellular network. Over-the-air software updates—which are possible for any vehicle that has built-in Wi-Fi capabilities—will reduce warranty costs, increase convenience for software recalls, and make it easier overall for customers and manufacturers to ensure that their software stays up to date. This will also reduce costs for OEMs and add value to vehicles and related products. Many auto manufacturers are already using over-the-air updates, and the practice will most likely become an industry standard and norm over the next five years.
- Collaborate and cooperate: Manufacturers should work in close cooperation and collaboration with both suppliers and customers in order to effectively deliver a product that meets customers’ needs and wants. This collaboration should begin as early as possible when developing a new vehicle or product so that the customers’ demands are clear and integrated into the rest of the development process and the supply chain. This will ensure that manufacturers do not waste time and money developing a product that customers will not find appealing and will help them to make appropriate procurement decisions.
- Cut material costs: The high price of raw materials is one of the biggest cost drivers in the automotive industry, accounting for almost half of the total cost of manufacturing a vehicle. Vehicle manufacturers’ dependence on these raw materials—especially steel—leaves them vulnerable to the negative effects resulting from global fluctuations and hikes in prices. To combat this, rather than simply maintaining their traditional supplier relationships, manufacturers should shop around for suppliers who will offer them the best price. As the industry shifts towards the use of aluminum, which is twice as expensive as steel but considerably more lightweight, reducing the cost of materials will become even more important, so auto manufacturers should begin to prioritize, make procurement decisions, and begin negotiations now.
Developing and Implementing Cost Reduction Strategies
Developing a comprehensive cost-reduction strategy is imperative for any organisation seeking to diminish production costs within the automotive industry. The initial step involves establishing precise and measurable goals and objectives, aligned with the SMART criteria – specific, measurable, achievable, relevant, and time-bound. Subsequently, it is essential to identify key metrics to gauge progress towards these goals, enabling effective tracking and necessitating any pertinent adjustments.
Following the establishment of these goals and metrics, a detailed plan of action, inclusive of specific steps and an implementation timeline, should be devised. Engaging all stakeholders, encompassing management, employees, suppliers, and customers, is crucial to ensure comprehensive consideration of all perspectives and alignment of the strategy with the organization’s overarching goals and objectives.
Executing the plan to reduce costs comes next, and it’s crucial to be aware of the methods used to ensure its success. Communication and training are vital at this stage because employees must grasp the objectives, measurements, and steps that make up the plan. Monitoring progress and making necessary adjustments is also important, and this can be accomplished through regular evaluations. Establishing a culture within the organization that is mindful of costs is also essential for carrying out the plan effectively.
This can be attained through training, communication, and rewards that promote frugal behavior. By nurturing a cost-conscious culture, employees are more likely to recognize and implement cost-saving measures independently, resulting in greater overall savings. These strategies are essential components in achieving sustainable cost reduction in the automotive industry.
Key strategies for saving costs in the automotive industry
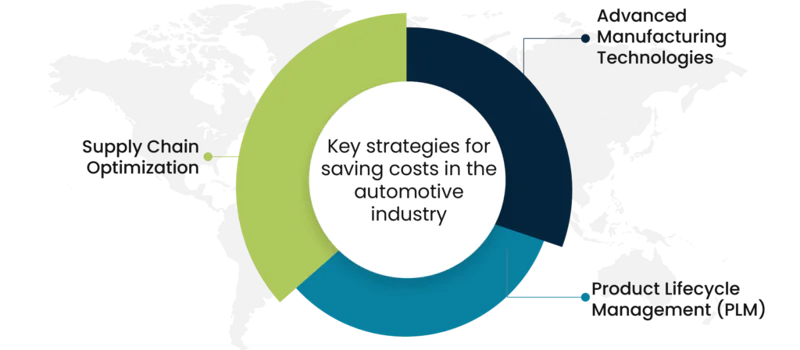
Supply Chain Optimization:
Explore and leverage global sourcing opportunities for components and materials. This involves identifying cost-effective suppliers globally and establishing strong partnerships to ensure a stable and cost-efficient supply chain. Implement lean principles to eliminate waste, reduce excess inventory, and improve overall production efficiency. This involves streamlining processes, optimizing production schedules, and minimizing downtime. Foster collaborative relationships with key suppliers. This can lead to better negotiation power, volume discounts, and improved overall supply chain efficiency.
Advanced Manufacturing Technologies:
Invest in automation and robotics to enhance manufacturing efficiency and reduce labor costs. Automation can lead to increased production speed, precision, and consistency, ultimately contributing to cost savings over time. Explore the use of 3D printing for prototyping and even production of certain components. This technology can reduce material waste and lead times, offering cost advantages in the long run. Implement predictive maintenance strategies using IoT (Internet of Things) technologies. This helps in identifying and addressing equipment issues before they lead to costly breakdowns, reducing downtime and repair expenses.
Product Lifecycle Management (PLM):
Incorporate cost considerations into the product design phase. This involves evaluating different materials, manufacturing processes, and assembly methods to identify cost-effective alternatives without compromising quality or safety. Standardize components and processes where possible. This reduces complexity, improves economies of scale, and simplifies maintenance and repair activities. Conduct thorough lifecycle cost analyses to identify areas where costs can be optimized over the entire product lifecycle, including manufacturing, maintenance, and disposal.
Identifying Cost Reduction Areas
To identify potential inefficiencies, automotive companies or even consultants hired by automotive companies must conduct an analysis of the production process. This in-depth analysis of the manufacturing process may take considerable time but will leave the manufacturer with an idea of what needs to be addressed. Gathering data is the first step in the process, including analyzing production schedules, performance metrics, equipment efficiency (OEE), and maintenance cycles. Analyzing this data will help the manufacturer identify and understand bottlenecks that delay the rest of the process. In addition to looking internally, manufacturers should also look externally to evaluate what other options there are for lower-tier suppliers. Supply chains have been stretched to their breaking point which have caused a dramatic increase in critical automotive suppliers, especially in the automotive industry. Manufacturers would be well-served by identifying critical suppliers and diversifying their upstream risk.
Moreover, to address supply chain disruptions, automotive companies must focus on acquiring efficient materials, optimizing the production process, and integrating automation where feasible. By conducting data analysis and implementing value stream mapping, companies can streamline their production facilities and enhance fuel efficiency. Additionally, considering factors like regional wages and exploring opportunities for outsourcing or offshoring can contribute to process optimization and cost reduction. Through continuous materials optimization and leveraging advanced data analytics, automotive manufacturers can achieve their goals and objectives while navigating the complexities of the modern automotive industry and ensuring the uninterrupted supply of auto parts.
Conclusion
In the automotive industry, optimizing production processes and reducing costs are paramount for sustainable growth and competitiveness. Leveraging strategies such as automation, outsourcing, and offshoring, coupled with data analytics and value stream mapping, enables manufacturers to identify inefficiencies and enhance operational efficiency. By prioritizing materials optimization and process optimization, automotive companies can achieve their goals and objectives while navigating challenges such as supply chain disruptions and fluctuations in regional wages.
Furthermore, embracing eco-friendly technology to improve fuel efficiency and reduce environmental impact is imperative. Collaborating closely with suppliers and embracing advancements in the automotive industry, including auto parts imports, ensures a sustainable future for production facilities and the supply of auto parts.