Creating a good budget is an essential part of any company’s planning and operations. However, despite it being such an important process, many organizations do not make full use of the resources and knowledge they have at hand. Procurement is deeply involved in spending, and yet is often left out of the budgeting process. There are many ways in which including procurement and supply chain management can benefit both the planning and execution of a company’s budget.
Budget and procurement
Budgeting plays a crucial role in procurement as it helps organizations effectively manage their financial resources. A well-defined budget ensures that procurement activities align with the overall financial goals and objectives of the organization. It helps in setting spending limits, prioritizing procurement needs, and making informed purchasing decisions. Budgeting also enables cost control, risk management, and accountability in procurement processes. By tracking and monitoring expenditures, organizations can optimize their procurement strategies, maximize cost savings, and ensure efficient allocation of resources.
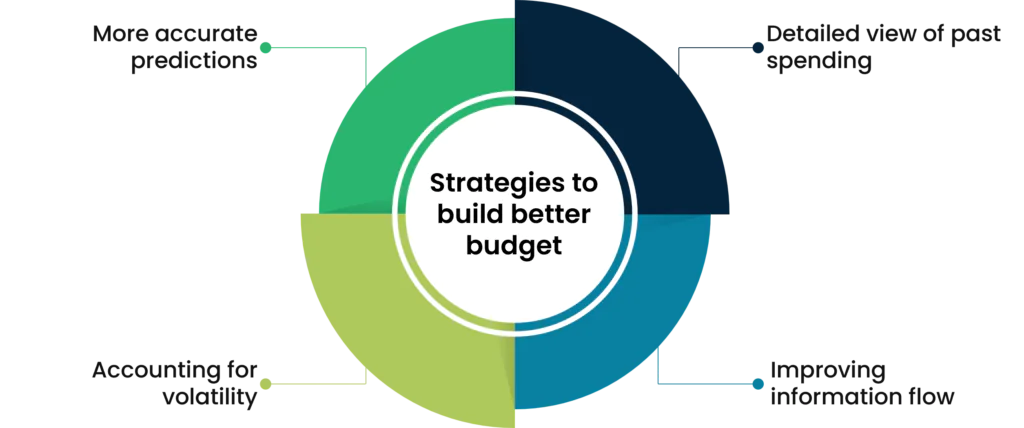
More accurate predictions
Procurement is the department responsible for finding suppliers, negotiating terms, and ordering supplies. As such, its members are best equipped to provide estimates of costs, and of the ease or difficulty of acquiring a given item. By consulting them while building the budget, it is possible to detect challenges and impractical plans before anything is implemented, potentially saving a considerable amount of money. Procurement can also point out if too little money has been allocated for a particular item, or suggest ways that money can be saved and budgeted elsewhere.
Detailed view of past spending
A solid procurement analytics solution can also be invaluable here. Rather than looking at the previous budget and tweaking it to suit future plans, it is possible to compare the previous year’s budget to that year’s actual spending. This can provide considerable insight into the accuracy of the budget, and allow the company to improve it for the next year. Even if the need for a particular supply is the same as the previous year, it is possible to make the budget more accurate simply by reviewing the last year’s costs for that supply. Also, by examining past spending, the company can identify areas where expenses are high and need to be reduced, or where they were lower than expected. Procurement can then take this information and look for ways to improve its terms with current suppliers, or look for new ones.
Accounting for volatility
Another benefit of including procurement is that the department can help plan for volatility in the supply chain. Procurement and supply chain has experience dealing with changing material costs, for example, and can give advice on how to account for that possibility in the budget. Fluctuating prices can have a greater impact on the company than one might realize. Oil prices, for example, affect the cost of transportation. There are other external factors that affect supply chain costs beyond the simple price of supplies, and procurement often has insight into these matters.
Improving information flow
If the department knows what and how much of a given supply the company expects to need in the coming year, it can plan accordingly. This can include actions such as finding additional suppliers if there is a greater need for a particular item, or renegotiating contracts in order to obtain more favorable terms.
Inviting procurement into the budget planning process produces benefits both in building the budget and in carrying it out. The supply chain has a substantial impact on the company as a whole, even if the company isn’t in the manufacturing industry. By taking advantage of procurement market intelligence and experience, it is possible to create a more accurate budget, plan for supply chain setbacks, and find the optimal way to carry out the company’s plans.
Here’s how you can access our procurement market intelligence
Reasons: Why there is a need for a procurement budget
Cost Control:
A procurement budget helps control and allocate funds for purchasing goods and services, ensuring that spending remains within planned limits.
Financial Planning:
It allows organizations to forecast and plan their procurement activities, ensuring that sufficient funds are available to meet purchasing needs.
Resource Allocation:
A procurement budget helps allocate resources effectively, ensuring that the right amount of funds is allocated to different procurement categories or projects.
Supplier Management:
It enables organizations to evaluate and manage supplier relationships by allocating budget for supplier selection, negotiation, and ongoing performance monitoring.
Risk Management:
A procurement budget helps identify potential risks and allocate funds for contingency planning, ensuring that unexpected events or disruptions in the supply chain can be managed effectively.
For more information on how procurement and supply chain can help in the budgeting process: