What is the supplier performance management process?
Supplier performance management (SPM) is the systematic monitoring and evaluation of the performance of suppliers engaged by a business. Effective management of supplier performance serves to exert control over expenditures, ensure adherence to regulatory requirements, and foster enduring partnerships.
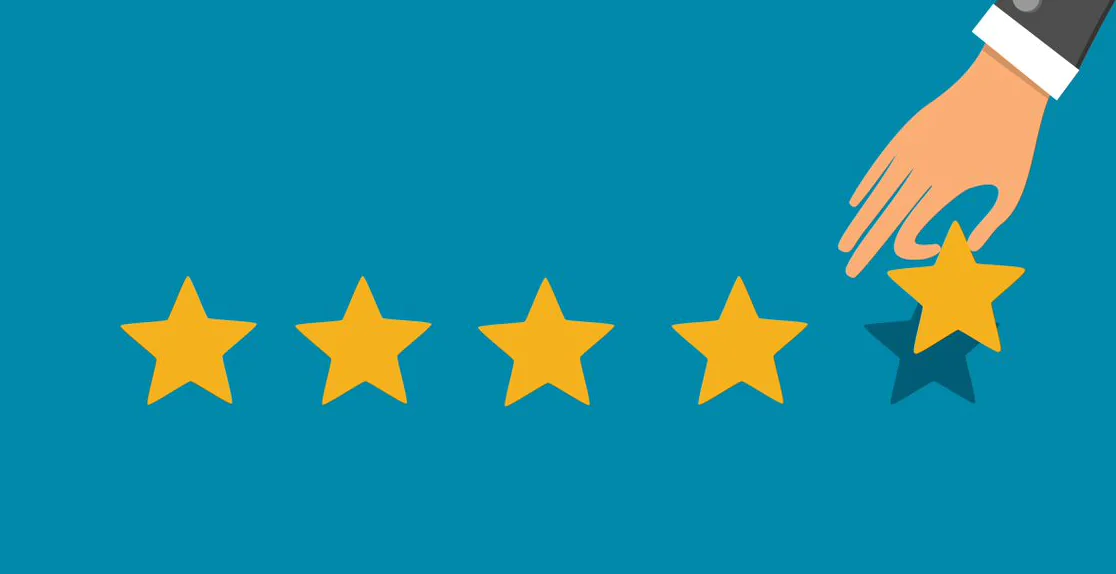
What is supplier performance management and its importance?
Monitoring and evaluating the performance of suppliers in terms of quality, punctuality, cost, and other important indicators is known as supplier performance management. It tries to improve product or service delivery, optimize supplier relationships, and reduce potential hazards. Through continuous monitoring and collaboration, businesses can ensure reliable and efficient supply chains, fostering better overall outcomes. Supplier performance management is crucial for maintaining consistent product quality, on-time deliveries, and cost control. It reduces risks, strengthens relationships, and enhances supply chain efficiency, contributing to business success.
Every company invests a considerable amount of time and effort in the supplier selection process, but in the long run, how do they evaluate if the supplier’s performance is meeting the desired standards? And how important is the measurement of supplier performance for a business? Almost all companies are already deploying some form of supplier performance measurement, be it in the form of key performance indicators (KPIs), or more sophisticated data gathering, and on-site assessment programs. Also, when businesses evaluate the performance of their supplier, the shortcomings in the adherence to standards can be easily detected; thus, promoting improvement.
Our SpendEdge professionals can help you with supplier performance management, here are the best solutions we provide
Here are seven steps to critically evaluate your suppliers, which can result in meaningful outcomes and better return on investment (Supplier management process)
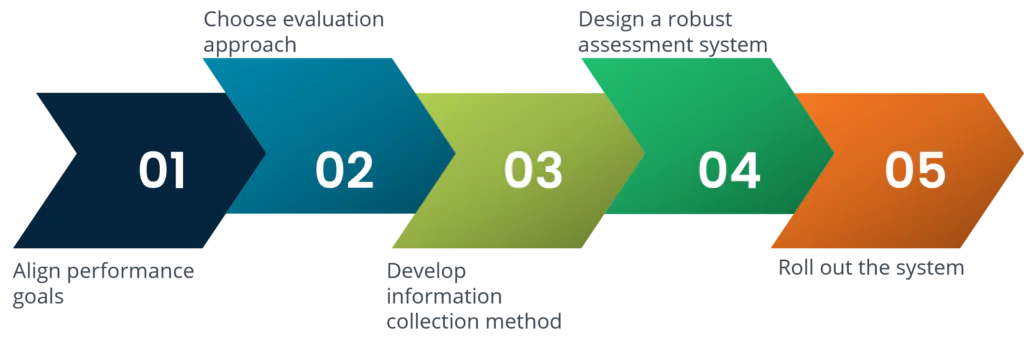
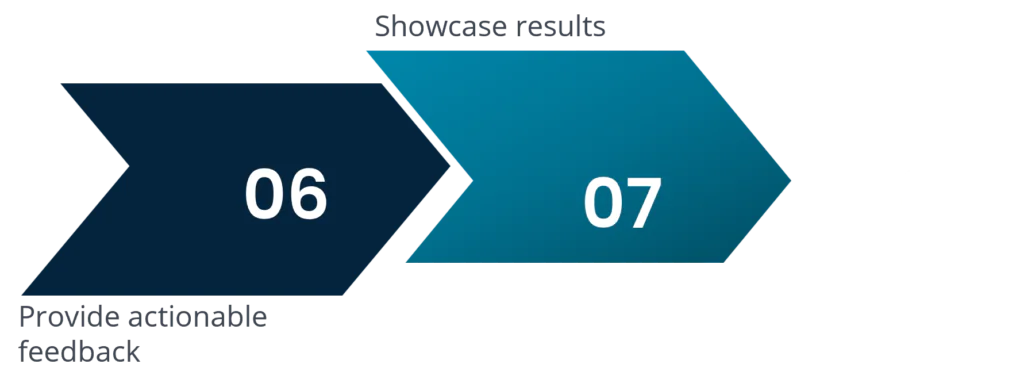
Align performance goals
Smart businesses must first have a clear-cut supplier strategy that relates to the overall organizational objectives and goals. In the long run, this will also help them to enhance their supply chain management. To achieve this, organizations can pursue continuous improvement programs and methodologies such as Six Sigma, lean enterprise, lean sigma, continuous improvement, operational excellence, and total quality management. Typically, companies trying to get to the next level of excellence need to have key suppliers aligned with their own organizational direction. Lack of synchronization in supplier activities and organizational goals can adversely impact cost, quality, and delivery.
Choose evaluation approach
Companies must evaluate some of these critical aspects of supplier performance, including financial health, operational execution, metrics business processes, and practices enabling behaviors or cultural factors risk factors. These factors can help review and understand the supplier’s readiness to comply with the organizational requirements and also efficiently meet the supply chain management requisites and guidelines. There is a need to establish key performance indicators for supply chain management which will help in evaluating the performance of every supplier or entity involvede in the supply chain.
Develop information collection method
The methods of information collection regarding the supplier performance include paper questionnaires, web-based questionnaires, extracts from current systems, site visits, and third-party standard certification. However, all these methods have their own challenges and complications. Companies must choose the method that best suits their purpose and gives them the optimal results.
Design a robust assessment system
No matter which components of a supplier performance assessment system an organization develops, a significant challenge lies in creating a system that is based on metrics both relevant to the business and based on generally accepted best practices. Designing and developing a robust supplier performance assessment system requires in-depth business knowledge, familiarity with high-performance systems, and expertise of measurement methodologies. Furthermore, it also requires expertise in adequately constructing the questions to elicit accurate responses and correctly measure performance.
Roll out the system
One of the most significant difficulties in assessment systems is the deployment. Primarily due to the vast number of challenges associated with each of the supplier assessment systems. Survey instrument development expertise, subject matter expertise, and knowledge of IT are needed to avoid the pitfalls in deploying all these approaches.
Provide actionable feedback
Customer companies need to have a real dialogue and discussion with their suppliers on performance and work on the critical issues of the performance. This requires a two-way flow of information. If the results of supplier performance measurement and supplier assessment are not actionable or expectations of actions are not communicated, those actions will not be put into practice.
Showcase results
Measuring supplier performance metrics is all about understanding, communicating, and then implementing the necessary corrective action for improving supplier performance. What companies need to do is to work with suppliers to develop action plans as a result of assessments. They should then track performance to these plans to close the loop and realize the full benefits of the supplier performance measurement process.
7 Key Steps to Monitor Supplier Performance
- Define Metrics: Clearly define the key performance indicators (KPIs) that align with your organization’s goals and supplier expectations.
- Establish Baselines: Set baseline performance standards against which supplier performance will be measured.
- Data Collection: Gather relevant data on supplier performance, including quality, delivery times, responsiveness, and compliance.
- Regular Evaluation: Conduct regular evaluations of supplier performance against established metrics to track progress over time.
- Performance Reviews: Schedule periodic performance reviews with suppliers to discuss strengths, weaknesses, and areas for improvement.
- Feedback Mechanisms: Provide actionable feedback to suppliers based on performance evaluations, and encourage open communication channels.
- Continuous Improvement: Collaborate with suppliers to develop improvement plans and strategies to address any performance issues identified during the monitoring process.
Supplier performance management challenges
• Implementing supplier performance management can be challenging due to the need to monitor an increasingly global and diverse supply base. It is crucial to define clear, relevant, and measurable KPIs that align with business objectives and supplier expectations. However, efficiently collecting and analyzing data to assess supplier performance can be complex, especially when dealing with numerous suppliers, diverse product lines, and a disconnected information landscape. Ensuring data access, accuracy, and consistency remains a significant hurdle as well.
• Another challenge is ensuring that suppliers are not resistant to performance management or that they do not consider the goals to be misaligned with their business. If suppliers do not consider the KPIs to be relevant to the relationship or find them cumbersome or unreasonable, they are unlikely to participate. Effective performance management requires participation from both sides. Without this buy-in, supplier performance management becomes an ineffective tactical reporting exercise that is done “to” suppliers instead of “with” them and does not drive improvement.
• Lastly, supplier performance management requires a significant amount of data across a large number of suppliers, which requires resources to implement and manage. Organizations may find it challenging to locate and allocate resources. This includes finding technology solutions to aggregate data, expose insights, and enable scalable processes and collaboration with suppliers.
Best practices: To achieve efficiency in supplier performance management
Technology solutions are instrumental in optimizing and elevating the process of supplier performance monitoring. Cutting-edge software and digital tools streamline the collection and analysis of performance data, ensuring precision and uniformity in tracking key performance indicators (KPIs). These solutions enable seamless performance evaluations by consolidating data in real-time, offering actionable insights into supplier metrics. Moreover, technology facilitates efficient communication and feedback loops, enabling timely and transparent interactions with suppliers. It fosters collaborative endeavors in formulating and monitoring improvement plans, providing platforms for shared access to documents and progress tracking. Furthermore, technology assists in maintaining comprehensive and well-organized records of all supplier-related activities and communications, crucial for future evaluations and decision-making.
To more about supplier performance measurement and ways to enhance your supply chain management
Conclusion
Effective supplier performance management is essential for optimizing supply chain operations and achieving organizational goals. By leveraging advanced technology solutions and adhering to best practices, businesses can streamline the process of evaluating supplier performance, enhance communication and collaboration with suppliers, and drive continuous improvement. From direct procurement to indirect procurement and services procurement, every aspect of the procurement process flow can benefit from robust supplier performance management practices. By centralizing data, conducting spend analysis, and implementing strategic sourcing initiatives, organizations can strengthen supplier relationships, mitigate risks, and maximize value across the supply chain. Additionally, the use of procurement software, e-procurement tools, and efficient inventory and contract management systems facilitates seamless operations and informed decision-making. Through proactive supplier management and a focus on performance optimization, businesses can achieve operational excellence and drive sustainable growth.