Supplier management is the systematic approach of overseeing relationships with suppliers to ensure they meet an organization’s needs and standards. It involves activities such as supplier evaluation, performance monitoring, negotiation, and collaboration to maintain a reliable and efficient supply chain. Effective supplier management helps optimize costs, quality, and overall supply chain performance. In today’s complex and fast-paced business environment, establishing a robust supplier quality management system is not only desirable but critical for sustaining compliance and achieving process excellence.
Companies must cultivate cordial relationships with global suppliers and build a supplier quality management procedure with well-defined metrics around quality and compliance. However, firms are mostly dealing with increasing regulatory oversight, intense competition, and market fluctuations. Managing supplier quality, therefore, takes a secondary position among organizations. They find it time-consuming and complicated to analyze data, uncover supplier insights, and gain a clear understanding of supplier capabilities. This results in data inconsistencies and deterioration of supplier performances.
What is Supplier Quality Management?
Supplier quality refers to a supplier’s ability to deliver goods or services that meet consumer needs and satisfy specifications. Supplier Quality Management involves overseeing the quality of goods and services provided by suppliers to mitigate reputational harm and compliance violations. It addresses issues like nonconforming material and defects, ensuring alignment with specifications and consumer needs. Through a collaborative and proactive approach, organizations implement Supplier Quality Management solutions to streamline quality processes, conduct audits, and uphold quality standards. This fosters transparency and efficiency in business processes, aligning goals with cost efficiency. By engaging qualified suppliers and addressing underlying problems like deviations and change requests, organizations ensure compliance, meet consumer expectations, and maintain contractor certifications.
What is Supplier Quality Management System?
A Supplier Quality Management System (SQMS) is a structured framework designed to ensure that suppliers meet established quality standards, continuously improve their performance, and contribute to the organization’s success. This system serves as a strategic tool for businesses to oversee, evaluate, and enhance the quality of products and services provided by their suppliers.
Importance of SQMS
Ensuring Alignment with Customer Expectations:
Supplier quality directly impacts the final product's ability to meet or exceed customer expectations. SQMS ensures that suppliers consistently provide products that are aligned with the desired specifications, thereby enhancing customer satisfaction and loyalty.
Minimizing Risks and Reducing Supply Chain Inefficiencies:
A well-implemented SQMS mitigates risks associated with poor-quality products, non-compliance, and delays. By establishing clear performance metrics and monitoring supplier activities, businesses can prevent disruptions, reduce waste, and streamline operations.
Continuous Performance Improvement:
SQMS fosters a culture of continuous improvement by regularly evaluating supplier performance. This evaluation goes beyond product quality and includes assessments of cost-effectiveness, delivery timelines, and compliance with regulatory standards, ensuring long-term competitiveness.
Cost Management and Value Addition:
Effective SQM processes help businesses control costs by identifying inefficiencies, minimizing defects, and reducing the need for rework. This, in turn, increases profitability while ensuring that the value delivered to customers is maximized.
Compliance and Regulatory Adherence:
With growing regulatory requirements across industries, SQMS ensures that suppliers adhere to legal and industry-specific standards. This not only avoids legal risks but also improves the organization’s reputation as a responsible and compliant entity.
Optimizing Supplier Relationships:
A robust SQMS facilitates transparent and collaborative relationships with suppliers. By providing regular feedback and sharing performance data, businesses can cultivate stronger partnerships, encourage supplier innovation, and drive mutual growth.
Wondering how your organization can minimize supplier risks and uncover supplier insights? Request a proposal to access our supplier quality management solutions.
Key Steps Involved in SQMS
Supplier management involves a multi-step process requiring collaboration, communication, and software tools to ensure efficacy. While we provide a foundational framework, it’s adaptable to suit your company’s unique workflows. The process unfolds in five key steps.
Firstly, approval entails establishing criteria for supplier approval, varying based on potential risk. Develop a master list detailing approval steps and roles/responsibilities, along with a checklist assessing vendor safety and quality systems. Audits, the second step, involve regular assessments to maintain supplier quality control. Larger companies may conduct second-party audits internally, while smaller ones typically opt for third-party audits, avoiding potential conflicts of interest. Utilizing supplier management software facilitates remote audits, document sharing, and electronic sign-offs for all business sizes.
The subsequent steps include incoming inspections, where raw materials and products are assessed for compliance, and ongoing communication, vital for maintaining positive supplier relationships. Lastly, handling non-conformance and CAPAs involves addressing deviations from quality standards and implementing corrective actions to prevent recurrences. Effective implementation of this multi-step process ensures consistent supplier quality management.
Business Benefits of SQMS
Minimizes risks
Extended supply chains, outsourcing, and globalization pose significant risk. These risks are usually related to quality, safety, business continuity, cost volatility, supply disruption, non-compliance, and many more. Having an effective supplier quality management process allows companies to effectively audit the supply chain and identify each specific risk. This helps businesses to reduce risks and avoid potential costly fallout.
Improves contract management and supplier relationships
For businesses to gain ground, companies must reduce costs, streamline contract management, protect brand reputation, and achieve long-term profitability. The process becomes much easier when tasks such as supplier prequalification, supplier audits, vendor management, insurance monitoring, and analytics are taken care of. With a robust supplier management process, companies can easily maintain good relationships with suppliers while carrying out supplier quality audits regularly. They can easily improve and grow a cross-beneficial business relationship.
Enhances procurement decisions
Most procurement decisions are under immense pressure to find, qualify, monitor, and manage suppliers while lowering the costs of doing so. With supplier quality management, CPOs can make informed procurement decisions by mitigating supplier risk through communication, evaluation, selection, and monitoring services. They can gain unprecedented visibility into safety statistics risk profiles and historical data. Moreover, improving supplier quality management can enhance the procurement process and reduce the lead time apart from maximizing data quality on the entire supply chain.
Meets compliance requirements
Businesses usually have to maintain compliance with, country-specific regulations, industry standards, and regulations, and corporate policies and standards. Working with a huge number of suppliers makes it difficult for companies to align with compliance standards. However, potential costs, disruptions, and damages can be avoided when a company is proactive in its approach to supplier compliance and supplier quality management.
Fosters sustainable performance
While most companies have strategies in place to manage health, safety, and behaviors within the organization, they fail to ensure the same with suppliers, contractors, and vendors. Supplier quality management actively fosters an aligned culture of health and safety through contractor prequalification, document management, auditing, employee-level qualification and training, business intelligence, and insurance verification.
Inability to analyze suppliers can impact the efficiency and procurement process of organizations. Stay a step ahead by talking with our experts to improve the supplier quality management process and gain specific insights.
Key Elements of Effective Supplier Management in Quality Management
-
Supplier Evaluation:
Thoroughly assess supplier capabilities, which includes evaluating their track record, production capacity, financial stability, and adherence to quality standards. A comprehensive evaluation helps identify reliable partners who can consistently meet quality requirements.
-
Supplier Selection:
Carefully choose suppliers based on the evaluation results and your organization's specific needs. Consider factors like cost, reliability, location, and the supplier's ability to align with your quality standards.
-
Clear Contracts:
Establish clear and comprehensive contracts that outline quality expectations, delivery schedules, pricing structures, and consequences for non-compliance. This contractual clarity is essential for ensuring that suppliers understand and commit to meeting your quality requirements.
-
Performance Monitoring:
Continuously monitor supplier performance to ensure they consistently meet quality and delivery standards. Implement key performance indicators (KPIs) and reporting mechanisms to track their performance, enabling timely intervention in case of deviations from established quality Foster a collaborative relationship with suppliers aimed at enhancing both quality and efficiency norms.
-
Continuous Improvement:
Regularly engage in feedback and improvement discussions to identify areas for enhancement, implement corrective actions, and optimize processes. This ongoing collaboration contributes to sustained quality improvements over time.
Supplier Intelligence Solutions: SpendEdge
- Tailored Solutions: SpendEdge offers customized supplier intelligence solutions to meet the unique needs of each client.
- Comprehensive Analysis: Our solutions provide in-depth analysis of supplier performance, market trends, and industry dynamics.
- Strategic Insights: Gain valuable insights to optimize supplier selection, negotiation strategies, and procurement processes.
- Risk Mitigation: Identify and mitigate risks associated with suppliers, supply chains, and market fluctuations.
- Enhanced Efficiency: Improve operational efficiency and drive cost savings through informed decision-making and proactive supplier management strategies.
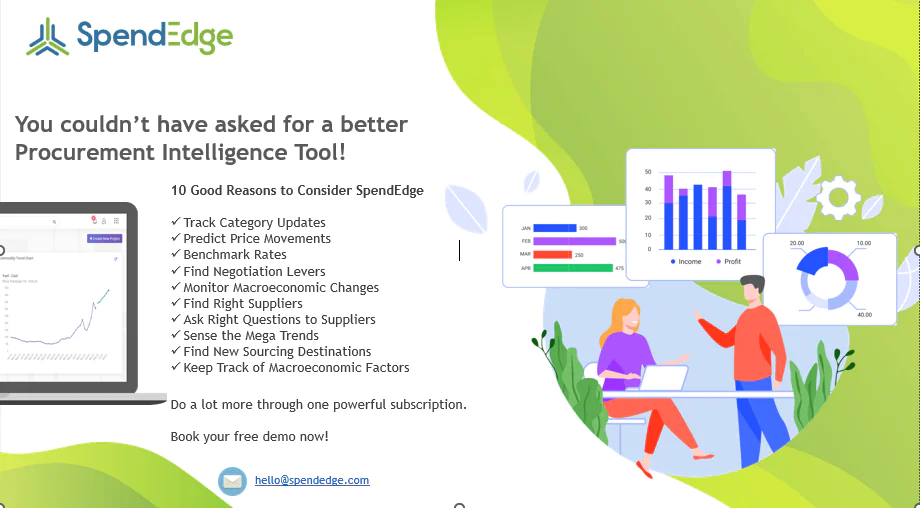
Conclusion
Effective supplier quality management (SQM) processes are essential for ensuring continual value addition to customers and surpassing their expectations in today’s fast-paced business environment. Procurement teams play a pivotal role in establishing robust supplier management processes that streamline operations, cut costs, and alleviate operational challenges. By implementing a centralized procurement approach and leveraging best-in-class practices, procurement leaders can optimize the procure-to-pay process, implement dual-sourcing strategies, and foster strong supplier relationships and partnerships.
This proactive approach to supplier quality management system implementation not only minimizes risks and ensures compliance but also enhances procurement strategy and overall general operation efficiency. Embracing these best practices in procurement enables businesses to meet compliance requirements, enhance procurement decisions, and foster sustainable performance, ultimately driving success in the ever-evolving marketplace.
Connect with our experts to implement a robust supplier quality management process tailored to your organization’s unique needs. Discover actionable insights, mitigate supplier risks, and drive operational excellence with data-driven strategies.